Core Technology
After years of technological innovation, the company has formed a core technology system for the entire production process of sintered neodymium iron boron magnets, covering multiple aspects such as magnet preparation, mechanical processing, surface protection, and regenerative manufacturing. By utilizing the core technologies mentioned above, the magnetic properties and service characteristics of the product can be improved, and resources and costs can be saved.
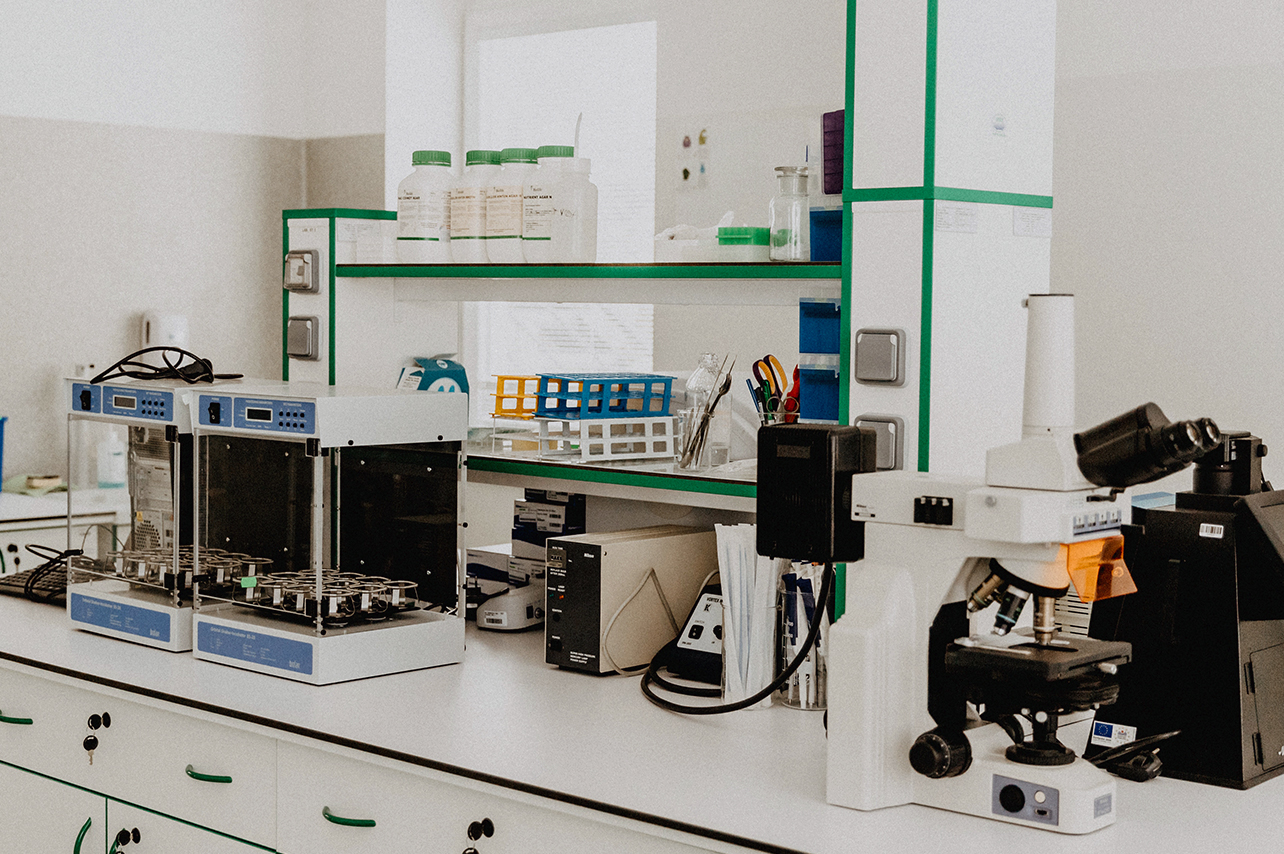
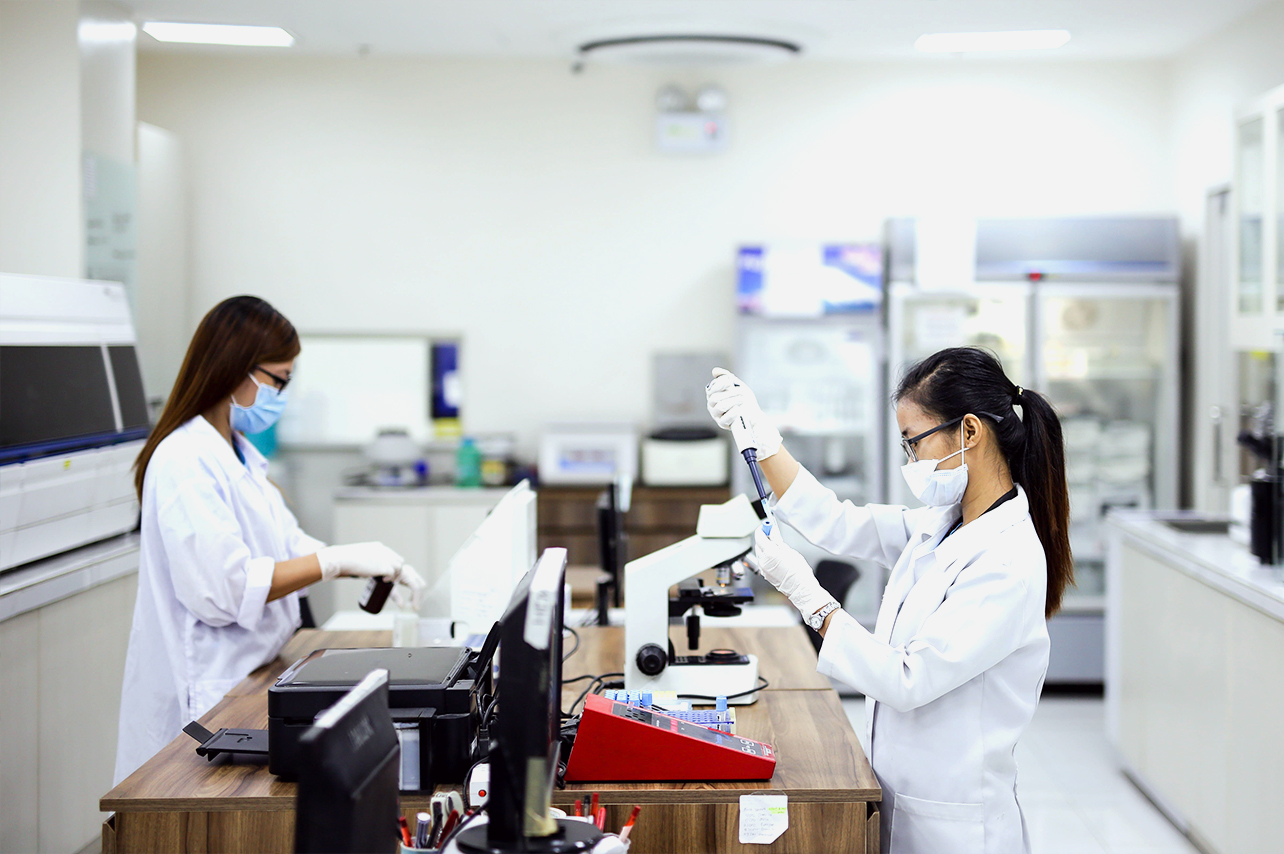
- 01: Grain boundary doping control technology
Progressiveness characterization
Sintered neodymium iron boron permanent magnet materials mainly consist of the main phase and grain boundary phases located between the main phase grains. Although the proportion of grain boundary phase in the material is relatively small, it largely determines the performance of the material and the final product.
On the basis of in-depth research on the influence of grain boundaries on the performance of sintered neodymium iron boron permanent magnet materials, the company has independently innovatively developed grain boundary doping control technologies for various substances. By directly introducing different types and quantities of substances into the grain boundary region of the magnet, it reacts with the original grain boundary phase during sintering and subsequent aging processes, changing the composition and structure of the grain boundary phase, thereby improving the performance of the magnet Reduce the amount of heavy rare earth added to high coercivity magnets.
The grain boundary doping control technology is a key core technology for the company to develop ultra-high magnetic performance series, high thermal stability series, and low weight rare earth series sintered neodymium iron boron magnets, and also a core technology for the recycling and regeneration process of waste magnets.
- 02: Whole process atmosphere control technology first
Progressiveness characterization
The performance of sintered neodymium iron boron permanent magnet materials is influenced by the content of nitrogen, oxygen, and carbon elements in the material. High nitrogen, oxygen, and carbon content consumes the rare earth elements in the material, leading to a decrease in the coercivity, temperature resistance, corrosion resistance, and other properties of the material.
The company has innovatively developed multiple control technologies and devices for nitrogen, oxygen, and carbon content in magnets, forming a full process atmosphere control technology in processes such as hydrogen crushing, airflow milling, magnetic field forming, sintering, and heat treatment. This effectively controls the nitrogen, oxygen, and carbon content in the magnets, reduces the consumption of rare earth elements, improves the utilization rate of rare earth elements, and improves the comprehensive performance of the product. While other performance remains basically unchanged, The average coercivity of the material increases by 5-10%, and the average corrosion weight loss of the material decreases by more than 20%.
The entire process atmosphere control technology is an important auxiliary technology for the production and manufacturing of the company's entire series of products.
- 03: Powder Surface Modification Technology
Progressiveness characterization
Sintered Nd-Fe-B permanent magnetic materials are produced by powder metallurgy process. Nd-Fe-B alloy micron powder is an important intermediate product in the production process of sintered Nd-Fe-B permanent magnetic materials. The properties of the powder largely determine the final performance of the magnet.
The company has innovatively developed a variety of Nd-Fe-B alloy powder surface modification technologies, including physical vapor deposition heavy rare earth metal film technology, powder surface diffusion modification technology, chemical synthesis film modification technology, etc. By surface modification of the powder, the flowability and oxidation resistance of the powder were improved, and the anisotropic field on the surface of the powder was increased, ultimately increasing the coercivity of the material.
The existing surface modification technology of neodymium iron boron powder in the industry mainly involves adding chemical reagents such as antioxidants and lubricants to improve the oxidation resistance and flowability of the powder, with less involvement in directly improving the coercivity of the material through powder modification. The powder surface modification technology developed by the company not only improves the flowability and oxidation resistance of the powder, but also enhances the anisotropic field on the surface of the powder, ultimately increasing the coercivity of the material, forming one of the key technologies for the preparation of high-performance sintered neodymium iron boron materials by the company.
- 04: New magnetic field orientation technology
Progressiveness characterization
Magnetic field orientation molding is a key process in the production and manufacturing of sintered neodymium iron boron. The consistency of powder orientation and the uniformity of compacted density after molding directly affect the main magnetic properties and mechanical processing yield of the magnet.
The company has carried out technological innovation in mold design, powder addition, orientation magnetic field, etc., and developed alternating magnetic field orientation molding technology that can improve the consistency of powder orientation, as well as powder addition technology that can improve the uniformity of powder filling and powder orientation consistency. It has designed and developed various new molds that can improve the consistency of magnet orientation and reduce the rate of magnet missing angles, Improved the main magnetic properties and yield of the company's high-performance sintered neodymium iron boron magnet products.
The industry mainly improves the consistency of powder orientation by increasing the strength of the oriented magnetic field and improving the fluidity of the powder. The company improves the consistency of powder orientation through integrated innovation of technology and equipment, and the improvement effect is better than the original method. Compared with the original method, the average increase in residual magnetism of the material is more than 0.2kGs, and the average increase in maximum magnetic energy product is more than 0.5MGOe. The new magnetic field oriented molding technology is an important auxiliary technology for the production and manufacturing of the company's entire series of products.
- 05: Grain boundary diffusion control technology
Progressiveness characterization
The composition and structure of grain boundary phases directly affect the multiple properties of magnets. By using grain boundary diffusion to introduce heavy rare earth elements into the surface of grain boundary phases and main phase grains, the coercivity of materials can be significantly improved without reducing residual magnetism.
The company has innovatively developed multiple grain boundary diffusion control technologies for sintered neodymium iron boron magnets, mainly including: deposition of heavy rare earth metal coating+diffusion technology on the surface of the magnet through electrodeposition, and deposition of heavy rare earth metal coating+diffusion technology on the surface of the magnet using laser cladding technology. The development and application of these technologies have significantly improved the coercivity of magnets and reduced the heavy rare earth content of high coercivity magnets, forming key technologies for the preparation of the company's ultra-high performance sintered neodymium iron boron magnets and low heavy rare earth sintered neodymium iron boron magnets. The common grain boundary diffusion control technology in the industry mainly includes two steps: contact between the diffusion source and the magnet to be diffused, and diffusion heat treatment. Compared with other grain boundary diffusion control technologies in the industry, the innovation of this technology is mainly reflected in the combination of the contact steps between the diffusion source and the magnet to be diffused with the surface protection steps of the magnet, achieving contact between the diffusion source and the magnet to be diffused while carrying out surface protection treatment.
- 06: New Efficient Green Surface Protection Technology
Progressiveness characterization
The main indicators for measuring the surface protection ability of neodymium iron boron magnets include adhesion to the substrate, corrosion resistance, wear resistance, etc. They are important service characteristics of magnets. To meet the different application needs of magnets, it is necessary to develop various efficient and green surface protection technologies.
The company has innovatively invented high corrosion resistance surface treatment technology for rare earth permanent magnet materials, developed coating adhesion improvement technology, corrosion resistance improvement technology, and wear resistance improvement technology, significantly improving the protective ability of existing coatings and meeting the application needs of numerous strong corrosive environments.
The company has innovatively developed various new surface green coating technologies and supporting devices for sintered neodymium iron boron magnets, including physical vapor deposition aluminum coating, spraying zinc aluminum coating, chemical synthesis temporary protective organic coating, laser cladding metal coating, fixtures for physical vapor deposition on the surface of sintered neodymium iron boron magnets, and automatic flipping devices for surface spraying of sintered neodymium iron boron block magnets, On the premise of ensuring that the protective ability of the coating layer is not lower than that of the existing coating layer, the environmental cost of protecting the surface of the magnet is significantly reduced.
- 07: Remanufacturing technology for waste sintered neodymium iron boron magnets
Progressiveness characterization
Rare earth is a non renewable strategic resource. The corner waste generated during the production and manufacturing process of sintered neodymium iron boron, as well as the discarded old magnets after use, contain a large amount of rare earth elements and are important secondary resources.
The company has independently innovatively developed surface decontamination technology after demagnetization of magnet oil and rapid removal technology of surface coating. By comprehensively utilizing independently developed grain boundary doping control technology, full process atmosphere control technology, and other magnet preparation technologies, the waste sintered neodymium iron boron magnets are directly regenerated to produce regenerated sintered neodymium iron boron magnets. Compared with the original magnets, the main magnetic energy recovery rate exceeds 95%, Realized the short process regeneration and manufacturing of waste sintered neodymium iron boron block magnets.
Compared with the commonly used waste magnet recycling technology in the industry, the recycling and remanufacturing technology developed by the company for waste sintered neodymium iron boron magnets has the characteristics of short process, high efficiency, environmental protection, and high recycling rate; Compared with ordinary magnets with the same performance, the regenerated magnets obtained from the remanufacturing of waste sintered neodymium iron boron magnets have lower production and manufacturing costs.